A WUR biochemist received a grant from the EWUU alliance to develop a new membrane that can absorb urea. This can diminish the water use of dialysis treatment, and may pave the way for a portable kidney device.
Researchers of TU Eindhoven, WUR, UMC Utrecht, and Utrecht University (together the EWUU alliance) are developing a membrane that could greatly improve the lives of kidney disease patients. Currently, patients need to visit the hospital 3-4 times a week for 4-hour sessions to undergo dialysis treatment. The haemodialysis machines are 100 kilograms and require a lot of water to extract the toxic compounds from the blood. This water needs to be purified and recirculated, which requires hospitals to employ a enormous wastewater treatment system. This is the main reason why it has been impossible to make the dialysis device portable.
The membrane to be developed by Akbar Asadi, assistant professor at Biobased Chemistry and Technology group, would improve water treatment, so that it requires much less water and pave the way for a portable dialysis device.
Waste water treatment
Although lifesaving, the dialysis treatment is not continuous and removal of urea is inadequate. This reduces the patients’ quality of life, and leads to a mortality rate of 10-15 percent per year. Dialysis happens through two membranes. Through the first membrane, toxic compounds such as urea are extracted from the blood and dissolve in water on the other side. The second membrane separates the toxic compounds from the water allowing recirculation of a small volume of water in the system.
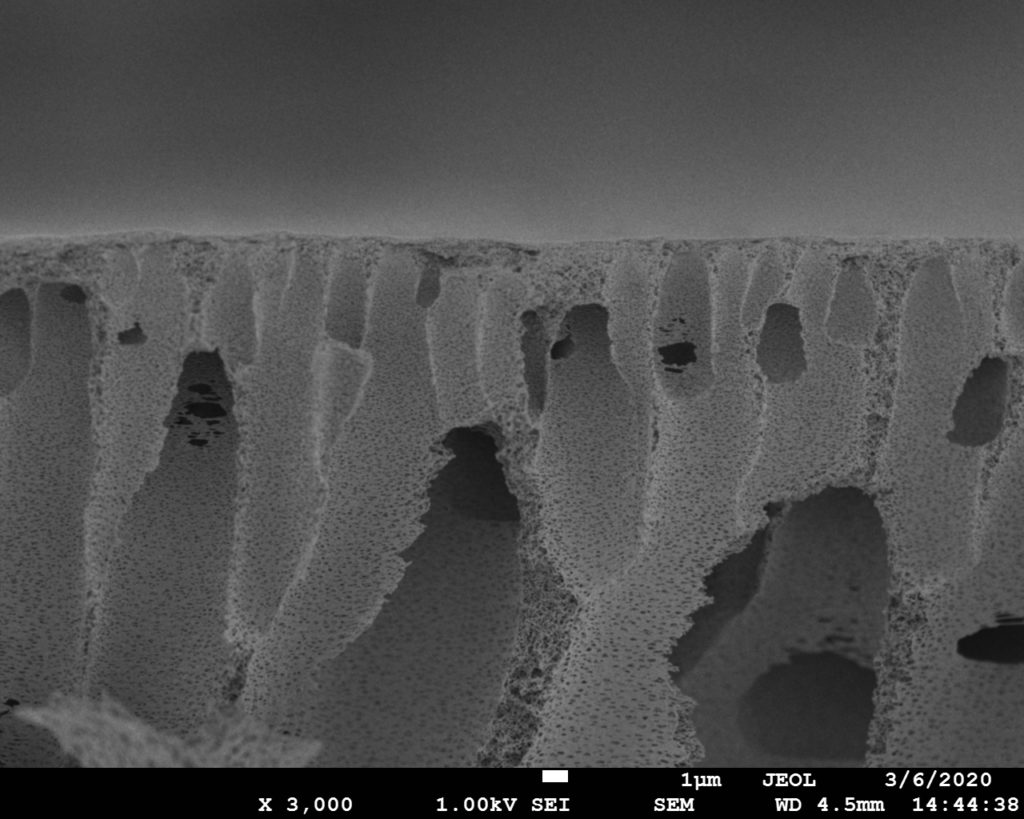
Membranes
Asadi’s project focuses on the second membrane. UMC Utrecht has developed beads that absorb urea. The bead material is based on polystyrene polymers. ‘We need to create a membrane from this absorbent material with a large surface area,’ explains Asadi. ‘Then little water is needed and the purification is instant.’ In this way, the membrane has a dual function: it binds the urea and sieves the water.
Simple method
The biochemist can easily produce polymer membranes in the lab, through a process called phase inversion. ‘First we dissolve the polymer in an organic solvent,’ Asadi begins. ‘Then we spread the solution as a thin film on a plate – a step called casting the membrane. Finally, we put it in water, where the membrane solidifies.’ The membranes will first be produced as flat discs. Later, the researches will make hollow fibre membranes, where the water passes through from the inside to the outside or reverse. ‘It should be robust enough not to break, but also have a high surface area to allow instant and efficient absorbance of urea.’
Plug and play
The aim of this first project is to build a proof of principle within a year, and then apply for a larger fund. The polymer absorbs urea through covalent bonds. These bonds are much stronger than hydrogen bonds or electrostatic bonds, and therefore it is hard to reuse the membranes once they are saturated with urea. Asadi envisions the eventual portable kidney device to contain a batch of several hollow fiber membranes, which the patient can ‘plug and play’ to replace an old membrane.