Normally the truck arrives within a defined time window at the cross-docking distribution centre to deliver its fresh meat or vegetables, which will quickly be loaded into another truck together with other fresh foods so that supermarkets are supplied. But this time the truck driver is half an hour late, due to traffic jams. As a result, seven out of ten trucks have already left to the supermarkets. Or the fresh product is less fresh than it looks because the cooling system of the delivering truck failed. When something goes wrong in the food supply chain, this lean system proves vulnerable. This vulnerability has increased in recent years. Transport of food has become more complex and time-consuming due to globalization; companies keep less stock to make business more profitable, and consumers ask for better quality and more variety of food. And with the precision timing of today’s leaner businesses , small hick-ups can have severe consequences. ‘Food companies should be prepared for these disturbances, but they are not’, says Jelena Vlajic. ‘Hitches in the system cost money. Take the amount of waste in the supply chain, because deliveries don’t meet the standards of the purchasing company. Vlajic made an inventory of the incidental disturbances that bother the companies and a framework to identify vulnerable spots in the supply chain. With this framework she made a vulnerability assessment method and a simulation model which can help food managers to deal with hitches and avoid or reduce the impact of disturbances. To make a Supply Chain Event Management System out of this method would take more effort, requiring an ICT company, for instance, to work it out, says Vlajic’s supervisor Jack van der Vorst. He stresses that there are no standard solutions for disturbances – solutions depend on the choices food companies make. They can reject products that don’t meet their standard and send it back, so the supplier has to pay. ‘In the end the costs for the supply chain as a whole are high and fewer products are available for sale’, says Vlajic. Normally they can choose between several suppliers – best price wins – but they also can make a partnership with one of them to be more secure about the quality and delivery times. Companies only do this when a product is very important for them, says Van der Vorst. The choices in risk management can differ in each company or product category, depending whether a company prioritized cost-effectiveness or responsiveness to customer needs. Vlajic’s method shows the consequences of both strategies – if something goes wrong
Weak link in the chain
Food companies usually deliver their fresh quality product on time to their customers. But sometimes a hitch occurs, which changes the generally quite lean and efficient food supply system into a vulnerable one. PhD student Jelena Vlajic developed a vulnerability assessment model to cope with these disturbances and make more robust food chains.
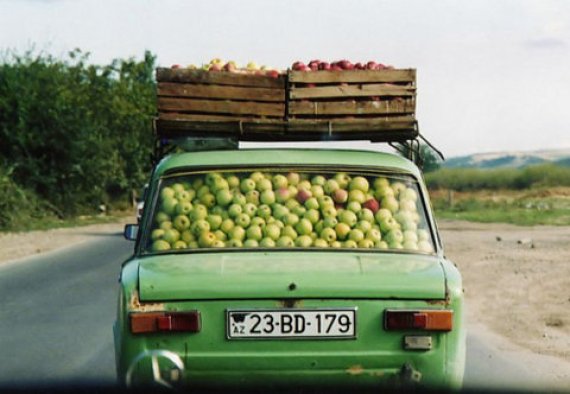